1.1 Overview
😋Electrolytic capacitors should be called electrolytic capacitors because one of the electrical stages of such capacitors is not a metal but an electrolyte or metal oxide. In short, the conductive carriers of this electrode are no longer electrons but ions. This is the basic characteristic of electrolytic capacitors. Now. According to the characteristics of electrodes, electrolytic capacitors mainly include aluminum electrolytic capacitors, tantalum, niobium electrolytic capacitors, and polymer electrolytic capacitors. Electrolytic capacitors are the most widely used type of capacitors in electronic circuits, and they are also the type of capacitors that encounter the most problems in applications. Therefore, it can be said that electrolytic capacitors are an eternal research topic.This article is an introduction of electrolytic capacitors
With the development of the times, aluminum electrolytic capacitors have gone through the primary stage. Today, it seems that there is a huge volume, the maximum operating temperature of 55 °C has developed to the miniaturization of electrolytic capacitors, the reduction of ESR, high ripple current, can withstand high temperature of 150 °C, and the maximum Capacitance reaches Farad level, surface mount and other new features. Aluminum electrolytic capacitors are no longer just for power frequency rectification, filtering and AC coupling. Aluminum electrolytic capacitors have entered every corner of the electronic circuit, and are responsible for power frequency rectification, filtering, bypass, and high-frequency rectification and filtering of power electronic circuits. Bypass of the wave current electronic circuit.
😛In the fields that aluminum electrolytic capacitors cannot enter, tantalum electrolytic capacitors play the role of aluminum electrolytic capacitors, which have good high-frequency characteristics, low ESR, and can withstand relatively large ripple currents.
Long life and stable performance. Tantalum electrolytic capacitors have also developed from the simple form of the year to ultra-low ESR with multiple anodes, which can withstand higher ripple currents; polymer tantalum electrolytic capacitors have the lowest ESR in the field of electrolytic capacitors. The solid cathode form makes tantalum electrolytic capacitors easy to implement in surface mount form, making an outstanding contribution to the miniaturization of electronic circuits.
😝One of the biggest disadvantages of aluminum electrolytic capacitors is high ESR. After using polymer negative electrodes, the ESR of aluminum electrolytic capacitors can be reduced by 1 to 2 orders of magnitude, which can withstand higher ripple currents and greatly increase the life.
1.1.1 The demand for large capacitance leads to electrolytic capacitors capacitors
🥳One of the main applications of capacitors is to smooth the pulsating DC current into a smooth DC current in the process of industrial rectification (this process can also be called filtering). For example, when converting sinusoidal alternating current into direct current, in order to smooth the rectified direct current, capacitor filtering is usually required, and the alternating current component in the pulsating direct current is “short-circuited” with the capacitor. However, smoothing the pulsating voltage from zero to peak value (1.414 times the rms value) to a near-smooth DC voltage requires a capacitor with a large capacitance. How big is the capacitor? Taking a single-phase bridge rectifier as an example, in a capacitor input filter circuit, generally, each rectifier diode can only be turned on for about 3ms to supply power to the output, and the output is powered by the filter capacitor for the remaining 7ms or so. At this time, the capacitor The energy storage will fluctuate by about 20%, that is, every half power cycle of the capacitor provides 20% energy storage to the output corresponding to 70% of the output power, In 1s, the capacitor needs the energy supplied to the output is
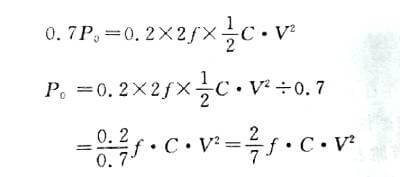
When the frequency f is 50hz,
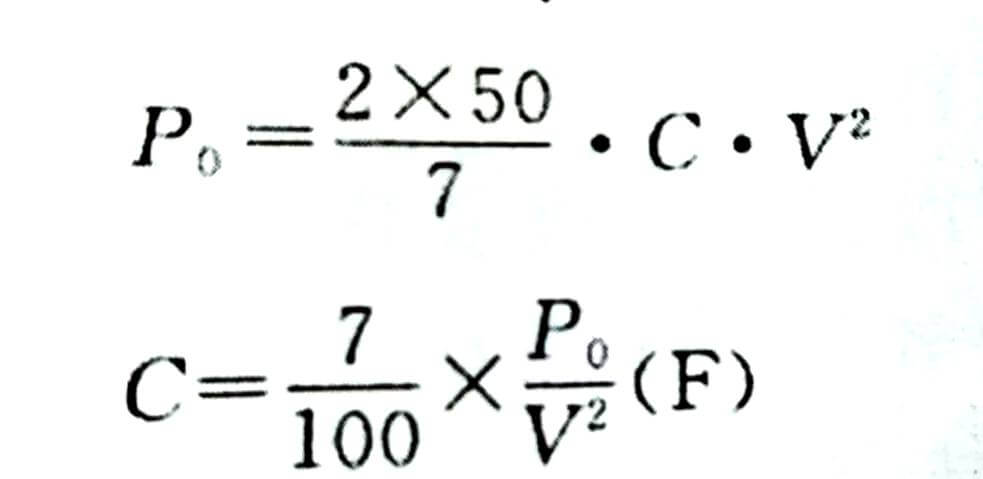
🎄Taking the AC 220V input direct rectification output voltage peak value of about 300V and supplying power to a 100W load as an example, the required capacitance is
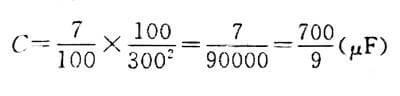
The capacitance is about 80uF, and the volume and price of an 80uF/400V film capacitor are unacceptable.
🌳Another example is 15/1A (the rectifier needs to have a voltage of 20V before the voltage regulator circuit, and the power is 20W) how much filter capacitor does the rectifier need?

A 3300uF/25V film capacitor would be sky-high.
💐For the above reasons, it is necessary to seek a capacitor with large capacitance, small volume and low price. In the first half of the last century when capacitor manufacturing technology was not very advanced, high-capacity capacitors were wanted. In the first half of the last century when the capacitor manufacturing technology was not very advanced, to obtain high-capacity capacitors, film capacitors and ceramic capacitors would be extremely expensive to realize and could not be put into use. Therefore, another way has to be found to obtain a capacitor realization method with high capacitance.
People naturally think of ways to increase the surface area of capacitor plates, such as roughening the surface of the plates, or making the plates porous like a sponge. The next question is, when one plate becomes rough or porous, how to make the other plate fit tightly with it and sandwich a dielectric material of uniform thickness and texture. These technical requirements are almost impossible for ordinary film capacitors and ceramic capacitors. Therefore, it is necessary to seek a medium and electrode form that meets this requirement, and electrolytic capacitors emerge as the times require under this technical and market demand.
1.1.2 Obtainment of Dielectric Thin Films
🌞The first problem of electrolytic capacitors is how to obtain a dielectric film with a uniform thickness and texture that is closely combined with the rough electrodes. One of the most commonly used metals in everyday life is aluminum. In order to increase the surface hardness and wear resistance of aluminum, anodizing is usually performed on the surface of aluminum. The surface hardness is increased by increasing the thickness of the aluminum oxide film. Solid alumina is a good insulator and has a very high dielectric constant (about 8). The dielectric strength is also very high (about 80 x V. So definitely a good dielectric material as well.
The aluminum oxide film with uniform thickness and texture can be obtained in the form of anodization, and the thickness of the aluminum oxide film can be precisely controlled by controlling the anodization voltage. Even with rough-surfaced electrodes, the thickness and texture uniformity of the aluminum oxide film will not be affected, and it will be in close contact with the aluminum. This has laid the most solid first step for the realization of aluminum electrolytic capacitors.
🍀In addition to aluminum, metals that can form oxide film dielectrics on metal surfaces by anodizing methods include tantalum, niobium, and titanium, which are collectively referred to as valve metals. In this way, the characteristics of forming a dense oxide film on the surface of aluminum or tantalum anodization method can be used, and aluminum oxide and tantalum oxide film can be used to form an insulating medium, because aluminum oxide is used. Tantalum oxide has high dielectric strength and a large relative dielectric coefficient (the relative dielectric coefficient is about 8 for aluminum oxide and about 20 for tantalum oxide, which is much higher than the dielectric coefficient of ordinary thin films of 2~3). The method of immersion makes the negative electrode of manganese dioxide and other forms of negative electrode, such as high-conductivity polymer and the medium in close contact with the positive electrode, also form close contact. therefore. Metal oxides such as titanium pentoxide and niobium pentoxide can also be good capacitor dielectrics.
1.1.3 Acquisition of rough electrodes
🐚Rough electrode surface is the most basic method for electrolytic capacitors to achieve large capacitance. Aluminum has good ductility, so aluminum foil can be used as the electrode of aluminum electrolytic capacitor. The etched foil that corrodes its positive aluminum foil to a very rough surface is shown in Figure 5.1.
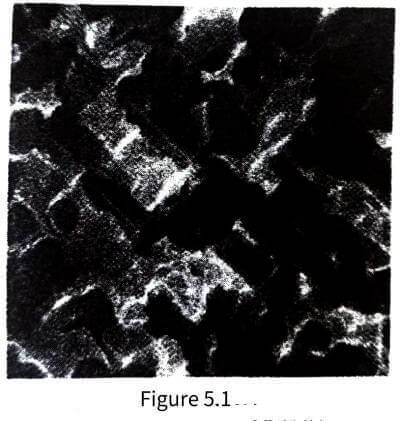
Except for aluminum, which has good ductility, other valve metals are hard and far less ductile than aluminum. Therefore, to use the remaining valve metal to form an electrolytic capacitor, it is usually necessary to press the valve metal in the form of particles into a porous metal block similar to the foamed plastic in daily life and sinter it. The sintered porous block structure can also increase as much as possible. surface area.
1.1.4 How to get the negative electrode
🌈Only by increasing the rough surface area of the positive electrode and the metal negative electrode can not actually increase the effective area of the electrode plate. Only the electrode plate of the negative electrode is as rough as the positive electrode, and the surfaces of the two electrodes are in close contact with each other, the effective increase of the electrode plate area can be achieved. If This would not be possible with conventional solid metal electrodes. In order to achieve close contact between the positive and negative electrodes under the rough surface, only one electrode can be solid metal, and the other electrode can only be non-solid or high method will make such a negative electrode, such as conductive liquid or gas, considering the gas The conductivity of the electrode is far inferior to that of the liquid, so the electrode should be a conductive liquid, so that the area of the two electrodes can be much larger than the geometric area of the electrode, which greatly increases the capacitance. Therefore, the capacitance of aluminum electrolytic capacitors and tantalum electrolytic capacitors It can be hundreds of times that of ordinary capacitors, and it is easy to obtain capacitances of hundreds of microfarads or even several farads, which cannot be achieved by general film capacitors.
However, it is undeniable that the solid electrolytes of liquid electrolytes are all particle conductive, and their electrical conductivity and temperature stability are not as good as those of metals that conduct free electrons. This is also one of the main reasons why the parameters such as equivalent series resistance and dissipation factor of electrolytic capacitors are inferior to those of film capacitors and ceramic capacitors with metal electrodes.
1.2 Basic knowledge of aluminum electrolytic capacitors
1.2.1 Structure of Aluminum Electrolytic Capacitors
⭐️The electrode structure of an aluminum electrolytic capacitor is shown in Figure 5.2. Among them, the anode aluminum foil is made of high-purity aluminum etched with many tiny tunnels to increase the contact area with the electrolyte. The enlarged part in Figure 5.2 is the microstructure between the two electrodes of the aluminum electrolytic capacitor.
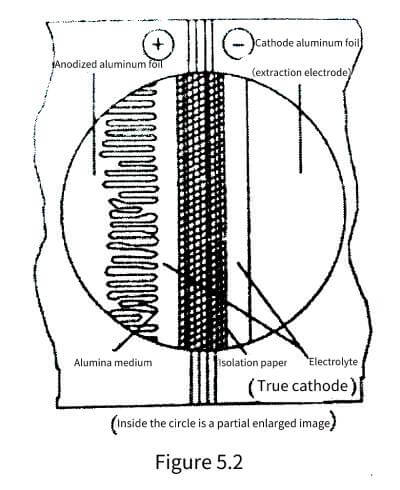
Aluminum electrolytic capacitors are formed by overlapping anode aluminum foil, separator paper and cathode aluminum foil, as shown in Figure 5.3, and then soaking in liquid electrolyte, so that the real anode is tightly attached to the anode of the anode and the anode of the electrolyte is in close contact with the anode. . Connect with leads (or bolts) at the outgoing end and install in an airtight container.
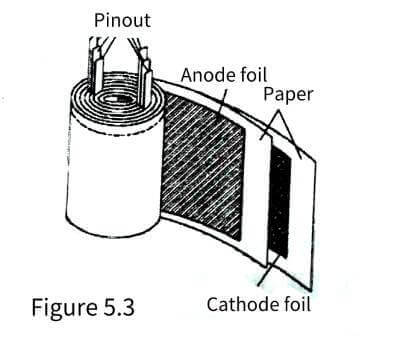
🌟The positive plate of the aluminum electrolytic capacitor is the anode foil; the dielectric electron is the aluminum oxide tightly supported on the anode foil; the real negative plate is a conductive liquid electrolyte, and the cathode aluminum foil is the lead-out electrode of the real negative electrolyte.
Since the surface area of the anodic aluminum foil after corrosion processing is hundreds of times its geometric area, and the thickness of the aluminum oxide dielectric is also less than 1um, the obtained capacitor has a huge plate area and a very close plate distance, so it can be obtained very large capacity. The capacitance can generally reach 2700000uF/6.3V, that is, 2.7F/6.3V (produced by CDE) and 10000uF/450V (produced by Jianghai Capacitor Factory). The rated voltage can cover the entire electrical range from low voltage 3V to high voltage 550V.
✨As can be seen from the above description, the usual capacitors have obvious winding structure electrolytic capacitors.
The positive and negative terminals are polar components and cannot be reversed.
1.2.2 A brief description of the manufacturing process of aluminum electrolytic capacitors
1.Corrosion
🔥The anode and cathode aluminum foils are composed of very pure and thin aluminum foils, ranging from 0.02 to 0.1 mm. Usually, the negative electrode foil is thinner than the positive electrode foil. In order to increase the panel area and capacitance, a very rough surface can be formed by etching the foil to increase the size. surface area, and close contact with very rough surfaces is achieved through the electrolyte.
2. Formation of alumina dielectric film through anodic evolution
🍒The dielectric of the aluminum electrolytic capacitor is overlaid on the anode foil. This medium is a thin layer of aluminum oxide that is electrochemically formed on the positive aluminum foil in a process called “anodizing”. The process is as follows: the positive electrode foil on the aluminum foil roll is passed through the electrolyte tank, and the direct voltage of the foil and the foil is continuously applied to complete the forming process. The voltage is 135%~200% of the rated voltage of the final capacitor, so the dielectric thickness of the aluminum electrolytic capacitor can be precisely controlled. Usually, the thickness of aluminum oxide is about 1.2~1.5nm per volt. For example, the positive foil of 450 V capacitor can form more than 600V, and the thickness of the oxide is 720-900 nm, which is less than 1/100 of the diameter of human hair.
Anodizing breaks down the effective anode foil surface area because particularly fine parts of the corroded foil can be blocked by aluminum oxide. The choice of foil and etching process can also be tuned by special etching modes, so that the microstructure of the low-voltage cathode can be fully utilized. The cathode foil is not anodized to maintain its surface area in close electrical contact with the electrolyte.
🍑Due to the brittleness of aluminum oxide itself, for example, the “too thick” aluminum oxide film will be brittle when the electrolytic capacitor is wound, resulting in many “weak points”, which will degrade the performance of aluminum electrolytic capacitors, which is why there is no rated voltage above 600 V. of aluminum electrolytic capacitors.
3. Cutting
🥭The 40~50 cem wide aluminum foil rolls are corroded and anodized, and then divided into the required size according to the length of the capacitor.
4. Riveting, winding
🍍The lead wires of the anode foil and the cathode foil are riveted or welded on the anode foil and the cathode foil. The anode foil and cathode foil are interposed between the separator papers, and are wound into a capacitor core (element) by a winding machine, and finally the shape is fixed with tape.
5. Saturate
🍊The core pack needs to be degassed, so the core pack needs to be vacuum-saturated with the electrolyte.
6. Seal
🍧The electrolyte is easily volatilized at high temperature, thereby reducing the effective area of the cathode. Therefore, electrolytic capacitors need to be sealed. In the 1960s or earlier, in order to reduce costs and reduce the amount of aluminum used (the output of aluminum was not high at that time and aluminum was mainly used for aircraft in China at that time), commercial-grade electrolytic capacitors (then called civilian products) were basically All wax paper tubes are potted with resin at both ends. Due to poor sealing, they will fail after a few years of use (sometimes it will fail completely in only one or two years. For example, the steamboat sound of a tube radio is a harmful coupling caused by the high AC impedance of the power supply. The resulting self-excited phenomenon is a manifestation of insufficient remaining capacitance after the electrolyte in the electrolytic capacitor volatilizes, and the severe hum not only informs the complete failure of the filtering electrolytic capacitor, and the operating temperature is only +55 ° C. The current electrolytic capacitor The core package is sealed in the container, and most of the containers are made of aluminum. Use a good sealing rubber stopper or rubber pad to add a resin plate at the container port and press it to soak it (as shown in Figure 5.4) to effectively prevent the volatilization of the electrolyte. To prevent the explosion caused by the gas pressure generated by the electrolytic capacitor during failure, the electrolytic capacitor with a diameter of more than 8mm is equipped with a pressure release device. Usually, K, > and X-shaped indentations are engraved on the end face of the aluminum shell to make the internal pressure of the electrolytic capacitor. Rupture and release pressure before opening the rubber stopper.
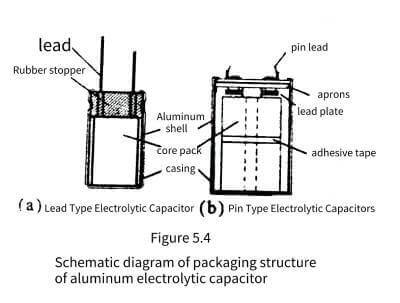
7. Aging
🍭The final step in the manufacture of electrolytic capacitors is aging, also known as energization. Its function is to repair the damage of the alumina dielectric film in the manufacturing process (especially the cutting of the anode aluminum foil and the riveting process of the lead-out electrode) by applying a forward voltage (similar to the anodizing process) to reduce electrolysis as much as possible. Defects in capacitors. This is the process of applying a DC voltage to the capacitor that is greater than the rated voltage but less than the original anodization voltage of the aluminum foil. Usually it should be at the rated temperature of the capacitor, but it can also be aged at other temperatures or even room temperature. Through aging, the damage to the aluminum oxide dielectric of the electrolytic capacitor and the corrosion of the aluminum oxide dielectric by chloride ions can be repaired. If the performance of the aged electrolytic capacitor (mainly leakage) still does not reach the target, it will be regarded as unqualified and removed from the product. This effectively reduces alkali or eliminates early failure (factory damage). Of course; the leakage current reaching the target is a sign that the aging is completed.
For users, it is also necessary to know the voltage, capacitance, parasitic parameters, leakage current, ripple current and heat, and life. These parameters and application considerations are discussed in detail below.
1.3 Basic parameters of aluminum electrolytic capacitors
🧬The basic parameters of aluminum electrolytic capacitors mainly include voltage, capacitance, maximum operating temperature and life, leakage current and loss factor. Some aluminum electrolytic capacitors, such as aluminum electrolytic capacitors for switching power supply output filtering, also have rated ripple current, ESR, etc. parameter.
1.3.1 Voltage
🦠The voltage indicators of aluminum electrolytic capacitors mainly include rated DC voltage, rated surge voltage, instantaneous overvoltage and reverse voltage, which will be introduced one by one below.
1. Rated DC voltage
🔋The rated DC voltage is the continuous working voltage allowed by the capacitor within the rated temperature range, which includes the sum of the DC voltage and the pulse voltage between the two electrodes of the capacitor. Usually, the rated voltage of aluminum electrolytic capacitors is marked on the surface of the capacitor. Usually rated voltage ≤ 100V is “low voltage” aluminum electrolytic capacitor, and rated voltage ≥ 150 V is “high voltage” aluminum electrolytic capacitor. The nominal voltages for the rated voltage are: 3 V, 4 V, 6.3 V, (7.5 V), 10 V, 16 V, 25 V, 35 V, (40 V), 50 V, 63 V, 80 V, 100 V, 160 V , 200 V, .250 V, 300 V, (315 V), 350 V, (385 V), 400 V, 450 V. 500 V, (550 V). The voltage values in parentheses are not common in our country.
2. Working voltage Vop
📿The working voltage is the voltage at which the capacitor is allowed to operate continuously within the rated temperature range. Over the entire operating temperature range, the capacitor can work continuously either at full rated voltage (including superimposed AC voltage) or at any voltage value between 0 V and the rated voltage. In a short period of time, the capacitor can also withstand The amplitude is not higher than a reverse voltage of 1.5V.
3. Reverse voltage
🔮Aluminum electrolytic capacitors are polarized capacitors and are generally not allowed to operate at reverse voltages. Where required, reverse polarity can be prevented by connecting a diode. Typically, diodes with a turn-on voltage of about 0.8 V are permissible. In a time shorter than 1s, the reverse voltage less than or equal to 1.5V can also be tolerated, but it is only for a short time and must not be in a continuous working state.
The harm of the reverse voltage is mainly that the reverse voltage will produce an electrochemical process that thins the aluminum oxide film, thereby irreversibly damaging the aluminum electrolytic capacitor.
4. Rated surge voltage Vs
🎈Rated surge voltage Vs. It is the voltage value that aluminum electrolytic capacitors can withstand in a short period of time: the test conditions are: the capacitor works at 25 °C, and the interval between two times is not less than 5min.
The relationship between surge voltage and rated voltage specified in IEC 384-4 is as follows:
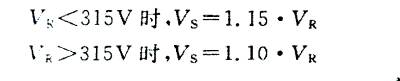
🎉Some aluminum electrolytic capacitors (mainly large aluminum electrolytic capacitors) are also marked with surge voltage on the case. The general standard method is: xxxVs.
5. Surge voltage measurement
🎇The specific test method for the rated surge voltage Vs of the capacitor is: at normal room temperature, aluminum electrolytic capacitors with capacitors below 2500uF can be connected in series with a resistance of 1000Ω±10%, and those with capacitance of 2500uF or higher should use Shenlian 2. 500000±10% resistance, in the cycle of 30s voltage on and 4min30s off, each capacitor discharges through the charging resistance or equivalent resistance. Repeat the cycle of 120h. The requirement to pass the test is that there should be no change in DC leakage current (DCL), equivalent series resistance (ESR) and dissipation factor (DF) values before and after the test, and there is no trace of mechanical damage or electrolyte leakage. Through this test condition, it can be seen that the time constant between the aluminum electrolytic capacitor and the series resistance is 2.5s, and 30s is 12 time constants. Such a long contact time can charge the aluminum electrolytic capacitor to the surge voltage value. 12 times per hour, a total of 1440 shocks in 120h. If the quality is not good enough, it will definitely fail after so many shocks.
6. Instantaneous overvoltage
🚤The limit overvoltage that aluminum electrolytic capacitors can generally withstand instantaneously. For aluminum electrolytic capacitors, transient overvoltage is usually an overvoltage condition that exceeds the surge voltage rating of the capacitor. This state will cause a large leakage current and enter a constant voltage state, and the voltage and current characteristics are very similar to the reverse characteristics of the Zener diode. If the capacitor cannot withstand this transient overvoltage, the capacitor may break down and fail. However, even if it can be tolerated, this state must not be maintained for a long time, because the pressure generated by the hydrogen gas generated by the capacitor will cause the irreversible pressure release device action (exploding) to make the aluminum electrolytic capacitor fail. Even if the pressure release device does not operate, this state will consume the electrolyte, and repeated occurrence of this state will shorten the service life of the aluminum electrolytic capacitor. Therefore, when the electronic circuit only needs a very short working life, the terminal voltage is allowed to reach the surge voltage or slightly lower than the instantaneous overvoltage in a sense.
The test standard of RIFA’s instantaneous overvoltage is: sharp pulse, the rise time is between 100us~5ms; the interval between two instantaneous overvoltages is greater than 5min: it can withstand up to 1000 instantaneous overvoltage shocks during the life period.
🎸In special applications (such as to withstand the impulse voltage of lightning strikes), special design methods can be used. For example, a transient voltage suppression diode clamp or a varistor with excellent performance can be connected in parallel at both ends of the aluminum electrolytic capacitor to successfully realize transient overvoltage protection.
The instantaneous overvoltage characteristics of aluminum electrolytic capacitors show that aluminum electrolytic capacitors can withstand instantaneous overvoltage (breakdown voltage) without damage, while other muon capacitors will be irreversibly damaged once the terminal voltage of other muon capacitors reaches the breakdown voltage value. This is also the “advantage” of aluminum electrolytic capacitors compared with other dielectric capacitors.
7. AC superposition, ripple voltage
🪂Not only DC voltage, but also AC superimposed voltage, or ripple voltage can be applied between the two ends of the aluminum electrolytic capacitor, but the following conditions must be met:
(1) The sum of DC voltage, AC superimposed voltage and ripple voltage does not exceed the rated voltage, and reverse polarity does not occur.
(2) The current does not exceed the rated ripple current.
1.3.2 Capacitance
🍸The capacitance indicators of aluminum electrolytic capacitors mainly include rated capacitance, electrostatic capacitance and the tolerance range of capacitance.
1. Rated capacitance
❄️Rated capacitance is the nominal capacitance, defined at 120Hz and tested at 25°C. The rated capacitance is also the single capacitance. Most of the nominal capacitance of the container is the E3 series priority value, which is 1.0uF, 2.2uF, 3.3uF, 4.7uF, 6.8uF; a few also use the E6 series value of merit, which is 1.0uF, 1.5uF, 2.2uF, 27uF, 3.3 uF, 3.9uF, 4.7uF, 5.6uF, 8.2uF; large capacity
Aluminum electrolytic capacitors also have some preferred values of E12 series, such as 18000uF.
2. Electrostatic capacitance
🌼The DC capacitance is obtained by measuring the charge when a DC voltage is applied to the capacitor. At room temperature, the capacity is slightly larger than that of AC, and it has better stability characteristics.
3. Capacitance measurement
🐾The capacitance of a capacitor can be obtained by testing its AC impedance or by measuring the amount of charge it can hold under a DC voltage. The two methods produce slightly different results. Generally speaking, the capacitance value (DC capacitance) measured by the DC voltage test method is slightly higher than the capacitance value (AC capacitance) measured by the AC current method.
In order to be consistent with the most common applications (such as rectification filtering or DC blocking coupling), the most common test frequency for the AC capacitance of aluminum electrolytic capacitors is generally 2 times the frequency of 50 Hz or 60 Hz power frequency AC, ie IEC384-1.IEC384- 4: The frequency given is 100Hz or 120 Hz. This is measured by the special test method given in IEC384-1 and IEC384-4.
🐋An AC voltage detection current of ≤0.5V can be applied to the aluminum electrolytic capacitor (will not cause reverse breakdown of the aluminum electrolytic capacitor), according to the real system of capacitive reactance and capacitance at a fixed frequency and capacitive reactance and voltage current The relationship C=1/(<2 ᶯf.V) can determine the capacitance. The AC capacitance can vary by more than 10% with temperature at most, and it also decreases with increasing frequency. Therefore, IEC384-1 and IEC384-4 give the basic test conditions when the frequency is 100Hz or 120Hz and the temperature is 20°C. The test method for testing the capacitance of general capacitors can also be used, and the bridge circuit for measuring the capacitance is used. When 1Vrms is applied on the power supply side, the maximum AC signal voltage is a 120Hz sine wave voltage without DC forward bias voltage without higher harmonics and subharmonics. Although the peak value of the power supply voltage is close to 1.5V, the voltage divider through the bridge circuit , the peak voltage applied to the aluminum electrolytic capacitor will be lower than 1 V and will not cause damage to the aluminum electrolytic capacitor. Generally speaking, aluminum electrolytic capacitors are mostly used for filtering, bypassing and DC-blocking coupling after rectification. These applications do not require high capacitance value and accuracy, and their capacitance tolerance (accuracy) is mostly ±20%. meet the requirements.
In some applications (such as discharge circuits and timing circuits) the DC capacitance will play a decisive role. This requires the measurement of DC capacity, usually by means of charge/discharge. According to the relationship between capacity and charge, voltage and charge and current, constant current charge/discharge is used, using C=(I.t)∆Vc, by detecting t to get the power C. Therefore, when the precise DC capacity is required
🐣It is best not to use aluminum electrolytic capacitors. In order to obtain a more accurate capacitance, multiple capacitors can be used in parallel to obtain a more accurate capacitance.
However, there are some exceptions where the DC capacity needs to be determined. 1 The EC publisher did not give any relevant instructions, therefore, a separate DIN standard was established. This standard DIN 41328 describes the test methods for one-time, non-cyclically charged capacitors.
4. Capacitance Tolerance
🌺Capacitor tolerances are the minimum and maximum allowable capacitance values expressed as a percentage of the nominal capacitance reduction and increase ∆°C/°C, typical capacitance tolerances are ±20%, -10%+50% and -10%+75%. The tolerance of high-voltage capacitors can be made relatively small, such as greater than 150 V. The general tolerance can be made less than ±10%. Capacitance varies with temperature and frequency, usually this change should also be within the capacitance tolerance range, usually this change itself is also affected by the voltage rating of the capacitor and the size of the capacitor.
1.3.3 Leakage current
1. Causes of leakage current and necessity of reduction
🦑Due to the particularity of the alumina dielectric as an insulating layer, the alumina dielectric is damaged during the cutting and riveting process of the aluminum foil or corroded by chloride ions in the electrolyte, resulting in defects. Patching, therefore. Even if DC voltage has been applied for a long time, there will still be a small patching current flowing, this current is called Current isolation (DCL)
The low leakage current means that there are very few fluoride ions in the electrolyte, and good compensation results can be obtained, and it also shows that the alumina dielectric as the insulating layer is well insulated. The iron and copper ions in the electrolyte and the aluminum foil will generate a galvanic effect current after applying a voltage to the electrodes of the aluminum electrolytic capacitor, which requires more charge to be consumed.
🦐The reason why it takes a long time for the “leakage current” to drop to a normal value. This observation also illustrates the “necessity of aging” for aluminum electrolytic capacitors before leaving the factory.
2. Measuring method of leakage current
🦀The test method and test conditions for leakage current of aluminum electrolytic capacitors are:
At 25 C, the capacitor under test is connected in series with a 1000Ω protection resistor to the rated voltage, and the leakage current is measured. After applying the voltage for 5 minutes, the leakage current does not exceed the maximum value in the specification. Small-capacity aluminum electrolytic capacitors can use 1 minute test results, and large-capacity aluminum electrolytic capacitors will require longer test times. Figure 5.5 shows the relationship between the current and time of the series resistance of the aluminum electrolytic capacitor connected to the DC voltage.

🐡As can be seen from the characteristic curve, the current will infinitely approach the final “leakage current” value – the current value required to repair the alumina dielectric.
The leakage current of aluminum electrolytic capacitors can be obtained by calculation, such as EPCOS aluminum electrolytic capacitors can be calculated by the following formula.
LL class:

GP class:

🐟Among them, I, C, and V are the working current, rated capacitance, and rated voltage, respectively. This result is at rated voltage at 20°C.
1.3.4 Dissipation factor
The dissipation factor (DF) of an electrolytic capacitor can be understood as the reactive power of the electrolytic capacitor and the active power of the equivalent series resistance (ESR) under the excitation of alternating current:
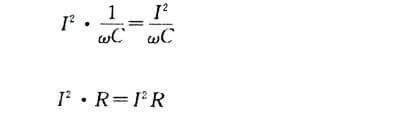
🦌According to the original definition equation (1.23) of the dissipation factor of the capacitor, substituting equations (5.11) and (5.12) into equation (1.23), we get
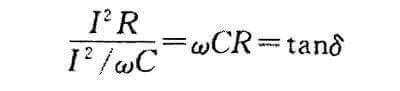
Obviously, this is the ratio of capacitive reactance to equivalent series resistance (ESR). Since equation (5.13) is very similar to the RC circuit in the AC circuit, and this ratio is very similar to the opposite side of the trigonometric function – the tangent function. Therefore, the dissipation factor (DF) of electrolytic capacitors is also called loss tangent (tanδ) in many technical literatures, as shown in Figure 5.6.
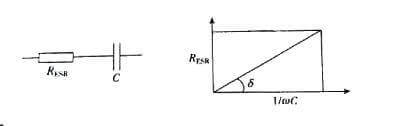
🌓It can be seen from equation (5.13) that as the frequency increases (that is, ω increases), ωCR increases accordingly, that is, the loss factor of the aluminum electrolytic capacitor becomes larger with the increase of the measurement frequency.
Since the test standard for the loss factor of capacitors was first proposed by the country using the frequency of 60Hz, the test frequency of the loss factor of capacitors is 60Hz AC full wave or the lowest ripple frequency after bridge rectification (twice the frequency of 60Hz) 120Hz. The test value of this test condition is 20% larger than the loss factor of our country’s 50Hz grid frequency.
☃️DF measurement is performed at 25°C, 120Hz, no forward voltage bias, maximum AC RMS 1V signal voltage tuning conditions. The DF value is determined by temperature and frequency.
1.3.5 Operating temperature range and life
1. Operating temperature range
⚡️Since the aluminum electrolytic capacitor is the negative electrode of the electrolyte, the boiling point of the electrolyte will be reached as the temperature increases. Therefore, the boiling point of the electrolyte will be the insurmountable maximum operating and storage temperature for aluminum electrolytic capacitors. In practical applications, the maximum working temperature is 10~-20 K lower than the boiling point of the electrolyte: Similarly, it is also because the negative electrode of the aluminum electrolytic capacitor is the electrolyte. When the temperature is too low, the
The electrolyte will become viscous or even solidify, and aluminum electrolytic capacitors will not be used. Therefore, aluminum electrolytic capacitors also have upper and lower limits for operating and storage temperatures. The entire temperature range between the upper and lower operating/storage temperature limits is the operating temperature range of aluminum electrolytic capacitors.
🍕For relatively low-level commercial applications, aluminum electrolytic capacitors have a maximum operating/storage temperature and a minimum operating/storage temperature of +85°C/-20°C. If there are special requirements for low temperature. The minimum working temperature can reach a 40°C; if the working/storage temperature of aluminum electrolytic capacitors is relatively high, an aluminum electrolytic capacitor with a maximum working/storage temperature of 105°C is required; when encountering higher working temperatures, such as energy-saving lamps or car engines In cabin applications, the maximum working/storage temperature of aluminum electrolytic capacitors is required to reach 125°C or even 150°C.
It can be seen from the above analysis that the maximum working/storage temperature of lead electrolytic capacitors can be divided into: +85℃ for general applications, +105℃ for high working/storage temperature, and 125℃ or even 140℃ for very high working temperature changes, Five maximum operating/storage temperatures of 150°C.
2. Lifespan
🥓It is also because the negative electrode of the aluminum electrolytic capacitor is the electrolyte. As time goes by, the electrolyte will gradually dry out. When the electrolyte dries up to a certain extent. The actual effective area of the negative plate of the aluminum electrolytic capacitor will become significantly smaller, and the capacitance will begin to decrease significantly: accompanied by a significant increase in the ridge ESR. When the capacitance is small and the ESR rises to a certain level, the aluminum electrolysis
Capacitors will lose their usefulness. This marks the end of life of aluminum electrolytic capacitors.
🥒According to the compromise of application environment and cost, aluminum electrolytic capacitors of different specifications have different lifespans.
3. Rated temperature and life rated parameters of aluminum electrolytic capacitors
🍍To sum up, the rated temperature of the aluminum electrolytic capacitor is the maximum temperature that the aluminum electrolytic capacitor is allowed to work and store. According to the working environment temperature requirements, it can usually be divided into five temperatures: 85°C, 105°C, 125°C, 140°C and 150°C Grade, life hours at each temperature grade, such as 1000 h, 2000 h, 3000 h, 4000 h, 5000 h, 8000 h, 10000 h or even higher.
1.3.6 Equivalent series resistance
🍥The equivalent series resistance (ESR) of electrolytic capacitors is shown in Figure 5.6, where the resistance of the electrolyte is the main part of the equivalent series resistance (ESR) of aluminum electrolytic capacitors. Aluminum electrolytic capacitors with low equivalent series resistance actually use low resistivity electrolytes.
The measurement of ESR is the resistance measurement of the equivalent series circuit of aluminum electrolytic capacitors under the environment of 25 °C with a maximum AC signal voltage of 1 V rms and a 120 Hz power supply with no forward bias voltage.
🎂For general aluminum electrolytic capacitors, most aluminum electrolytic capacitor manufacturers do not give ESR data, but for low ESR aluminum electrolytic capacitors used in switching power supplies or pin-type aluminum electrolytic capacitors with relatively large capacitances, this data is given.
The main reason why most aluminum electrolytic capacitor manufacturers do not give ESR data is that the ESR of aluminum electrolytic capacitors is too large compared to capacitors with other dielectrics. For example, 1uF/16 V ordinary aluminum electrolytic capacitor, its ESR is generally around 20Ω; 100uF aluminum electrolytic capacitor, its ESR is also between 1.5-2Ω. Just imagine, such data written in the data sheet will definitely affect the confidence of the users to use aluminum electrolytic capacitors. Therefore, in a certain way, the application of aluminum electrolytic capacitors is a helpless choice.
🍹In the application of switching power supply, it is often found that when ordinary aluminum electrolytic capacitors are used, the output voltage ripple and peak suppression effect is very poor. The main reason is that the ESR of conventional aluminum electrolytic capacitors is “too large”. In high frequency applications, it is a resistor for AC circuits. Therefore, in order to obtain a better high-frequency filtering effect, the ESR of the filter capacitor should be reduced as much as possible. That is, a low-ESR aluminum electrolytic capacitor should be selected. The ESR of low ESR aluminum electrolytic capacitors can generally be an order of magnitude or more lower than that of ordinary aluminum electrolytic capacitors. In order to obtain low ESR aluminum electrolytic capacitors. A low resistivity electrolyte should be used. If it is also necessary to reduce the equivalent series inductance, measures of low parasitic inductance should be adopted in the winding process and electrode lead-out of the aluminum electrolytic electrolytic device.
1.3.7 Rated Ripple Current
🍾The AC ripple current flowing through the aluminum electrolytic capacitor will cause loss on its ESR and cause the aluminum electrolytic capacitor to heat up. The limit of this heating limit to the ripple current determines the rated ripple current value. It is defined as the maximum ripple current value that can ensure the rated life time of lead electrolytic capacitors at the highest operating temperature. For aluminum electrolytic capacitors for general applications, most manufacturers do not provide rated ripple current data, but for low-ESR aluminum electrolytic capacitors used in switching power supplies or pin-type aluminum electrolytic capacitors with relatively large capacitances, this data is given. In fact, the ripple current that aluminum electrolytic capacitors can withstand is relatively low. For general-purpose aluminum electrolytic capacitors, the first impression of the acceptable ripple current value is that it is very low. Fortunately, most applications do not require high ripple current.